5 Basic Weld Joints & How To Maximize Results
Understanding the Basics of Joint Design
A well-executed joint design adheres to specifications outlined in welding codes and standards, essential in professional welding practices. It dictates the type of weld an operator must execute to meet the acceptable quality standards.
Discover more about the five fundamental types of weld joints along with valuable welding tips for each type to optimize results!
- Butt Joint: Commonly used in sheet metal and pipe welding, it involves joining two pieces of metal end to end. The surfaces are often shaped or beveled to allow for deeper penetration of the weld. On thin sections, it’s often possible to make full penetration welds using a square butt joint. When welding on a thick plate or pipe, it can be challenging for the welder to get 100% penetration without some type of groove being used. (Bevels or V, J, U shaped grooves.) Projects using this design can include an exhaust system on a car, and joining panels for a door. Butt joints are renowned for their robust mechanical strength when fitted and welded accurately. Here's a breakdown of the various design options:
- Butt joints can be welded with or without backing material. The presence of backing material, often in the form of a backing bar or strip, enhances stability during welding. Conversely, an open root configuration is adopted when no backing material is used.
- When preparing workpieces for a butt joint, the meeting edges may necessitate different levels of preparation. No edge preparation results in a square joint design, creating what's known as a square groove. Alternatively, beveled edges are common in butt joints, either partially or fully throughout the material thickness, with specific bevel angles defining the edge preparation. This can result in a V-groove or single bevel configuration, depending on whether one or both workpieces are prepped.
- The edges of a butt joint can either touch directly or be spaced within a specified tolerance to create a root opening, impacting weld penetration and strength.
- The material thickness and application play a crucial role in determining edge preparation. While beveled edges typically result in stronger welds, they are more time-consuming and require additional weld deposit. Square grooves are preferred for thinner materials, such as sheet metal or those less than 1/8-inch thick, where extensive edge preparations are impractical.
- By understanding and optimizing these design variations, welders can ensure the integrity and performance of butt joints across diverse applications and material types.
- T Joint: As the name suggests, T joints are formed when two pieces are connected at a 90-degree angle, coming together to form a “T” shape. T-joints possess good mechanical strength, especially when welded from both sides. You'll find these joints in many fabrication applications, including structural steel, tubing and equipment applications.
- T-joints typically necessitate minimal joint preparation and can be welded with ease, provided the correct parameters and techniques are employed. You have the option to leave the joint edges untouched or prepare them by cutting, machining, or grinding.
- When welding a T-joint, it's crucial to position the weld on the side of the joint that will bear any stress. Weld failure can occur if impacts or loads are applied from the opposite side of the joint. To mitigate this risk, consider welding both sides to maximize strength, especially when stress will be exerted from multiple directions.
- T-joints stand out as the most prevalent joint design across various applications. They are relatively straightforward to weld in flat, horizontal, vertical, or overhead positions, unlike other joint designs that may pose challenges when welded out of position.
- For a T-joint with a 90-degree angle, it's advisable to adopt a 45-degree work angle to ensure adequate penetration on both workpieces. When welding dissimilar metal thicknesses using a T-joint, prioritize directing more weld onto the thicker material for optimal results.
- Corner Joint: Similar to T joints, corner joints involve joining two pieces at a perpendicular angle. The difference is corner joints meet at the “corner” creating an L shape. These types of joints are among some of the most common in the sheet metal industry, such as in the construction of frames, boxes and other applications. There are two ways of fitting an outside corner joint—either open corner or closed corner.
- When two metal pieces meet at a corner in welding, they can form either a closed or open corner joint. In a closed corner joint, one piece's edge aligns perfectly flush against the other. An open corner joint occurs when there's a visible gap at the corner, revealing the thickness of each metal piece. The choice between open and closed corner joints is often dictated by factors such as material thickness and the required strength for the application.
- When working with open corner joints, it's important to adjust welding travel speeds, particularly on thinner materials, to prevent burn-through. These joints typically take on a V shape and may necessitate additional weld deposition, depending on material thickness.
- Closed corner joints offer the advantage of allowing weld faces to be ground down for a smooth transition between the weld and base material.
- Achieving proper fit-up of workpieces is crucial for corner joint welding. Ensuring a precise 90-degree angle and considering potential distortion during welding are essential steps. Depending on how the joint is prepared, the angle may shift post-welding, leading to distortion. Using jigs or fixtures to secure parts in place can help minimize the risk of distortion effectively.
- Lap Joint: Essentially a modified butt joint, lap joints are formed when two pieces of metal are connected in an overlapping pattern on top of each other. They are commonly used to connect two pieces with different thicknesses together. Welds can be made on one or both sides of the work pieces for enhanced mechanical properties. Accelerated corrosion can be common due to moisture retention in the lap.
- Lap joints are commonly used for connecting plates or sheet metal, such as in vehicle flooring installation or hole patching.
- To determine the necessary overlap in the joint, consider the thickness of both workpieces; generally, thicker materials require greater overlap.
- When creating lap joints, ensure there are no gaps between the workpieces, aiming for a flush alignment. When welding lap joints on thinner materials like sheet metal, adjust your amperage downwards and increase your travel speed to prevent distortion and burn-through.
- When deciding between a butt joint and a lap joint, note that a butt joint yields a flush contour, aligning the workpieces in the same plane. In contrast, lap joints offer added strength in high-stress areas but result in more visible joints and lack a flush finish.
- Edge Joint: Formed by placing two pieces together along a parallel plane and joining the surface edges. One or both pieces can be formed on an angle. The main purpose of this type of joint is to join parts together so that stresses are distributed across the pieces.
- Various types of edge joints exist, depending on the preparation of the edges. They can be left square (square groove) or prepared by grinding, cutting, or machining into V-groove, J-groove, or U-groove configurations, similar to those used for butt joints. These preparations enhance the weldment by facilitating sufficient penetration or improving overall weld coverage in edge joint welding. Additionally, welding all sides of an edge joint can enhance rigidity.
- Edge joints and corner joints share many similarities. Typically, a corner joint refers to the outside of the workpieces, while an edge joint can be found on the inside. The choice between an edge joint and a corner joint often hinges on the specific application requirements and material thickness.
- In cases where aesthetics are crucial, edge joints may require post-weld grinding to achieve a flush weld with the base material.
Mastering joint design is key to producing welds that meet professional standards. By adhering to welding codes and understanding the nuances of each joint type, you can ensure your work meets quality benchmarks. With this knowledge and the right techniques, you can optimize your welding to achieve superior results.
If you are a business looking for professional fabricators to create your next project, reach out to us via our contact page or by giving us a call at 905-643-0016.
For more steel and fabrication insights check out our education center and follow us on LinkedIn for bi-weekly posts!
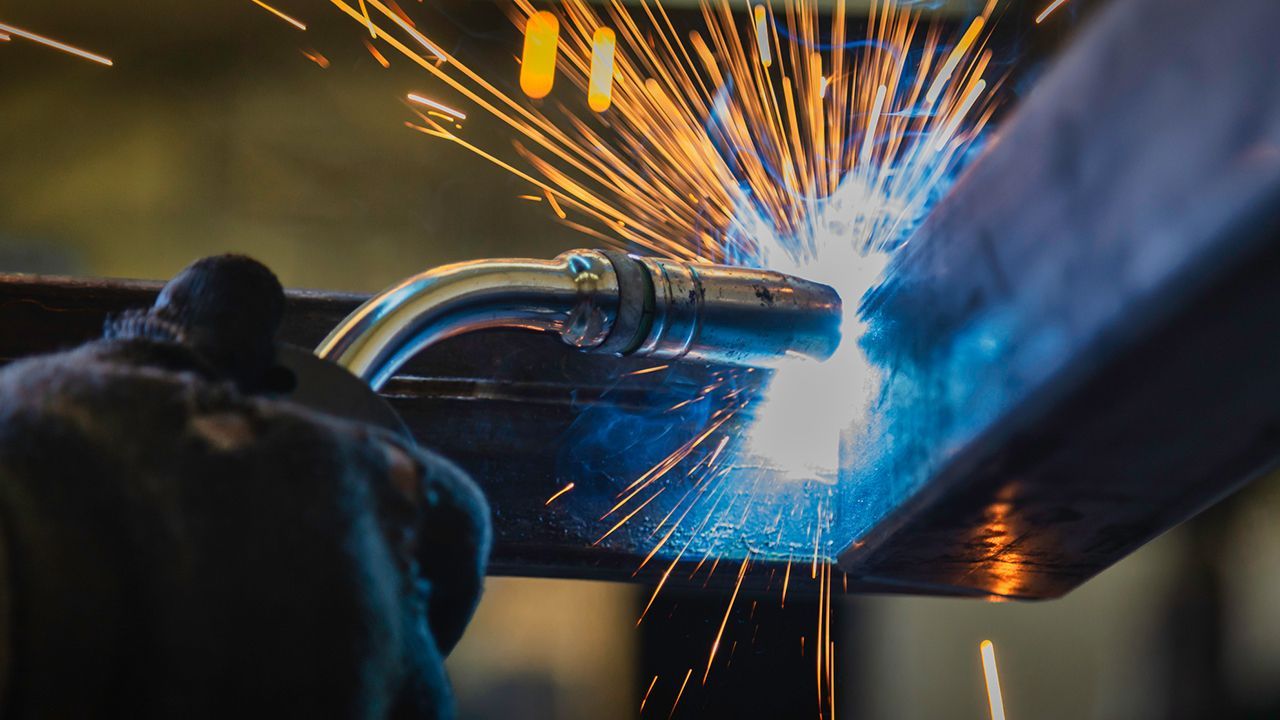
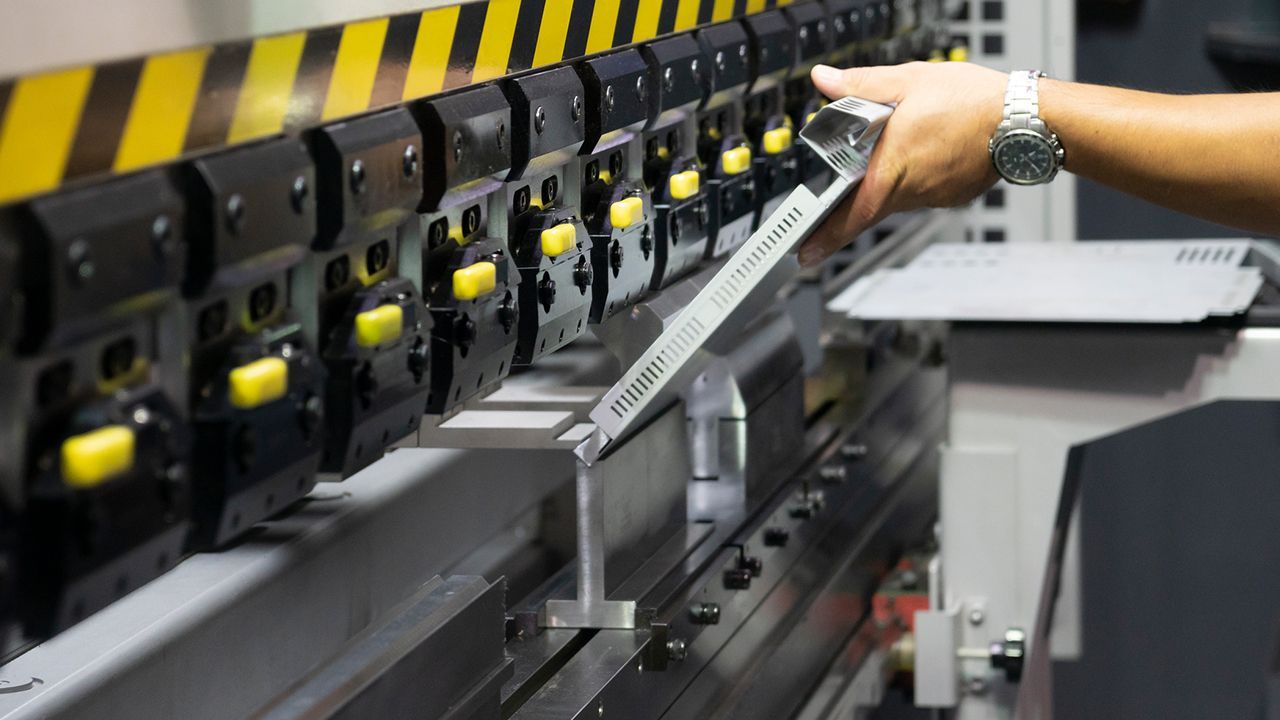
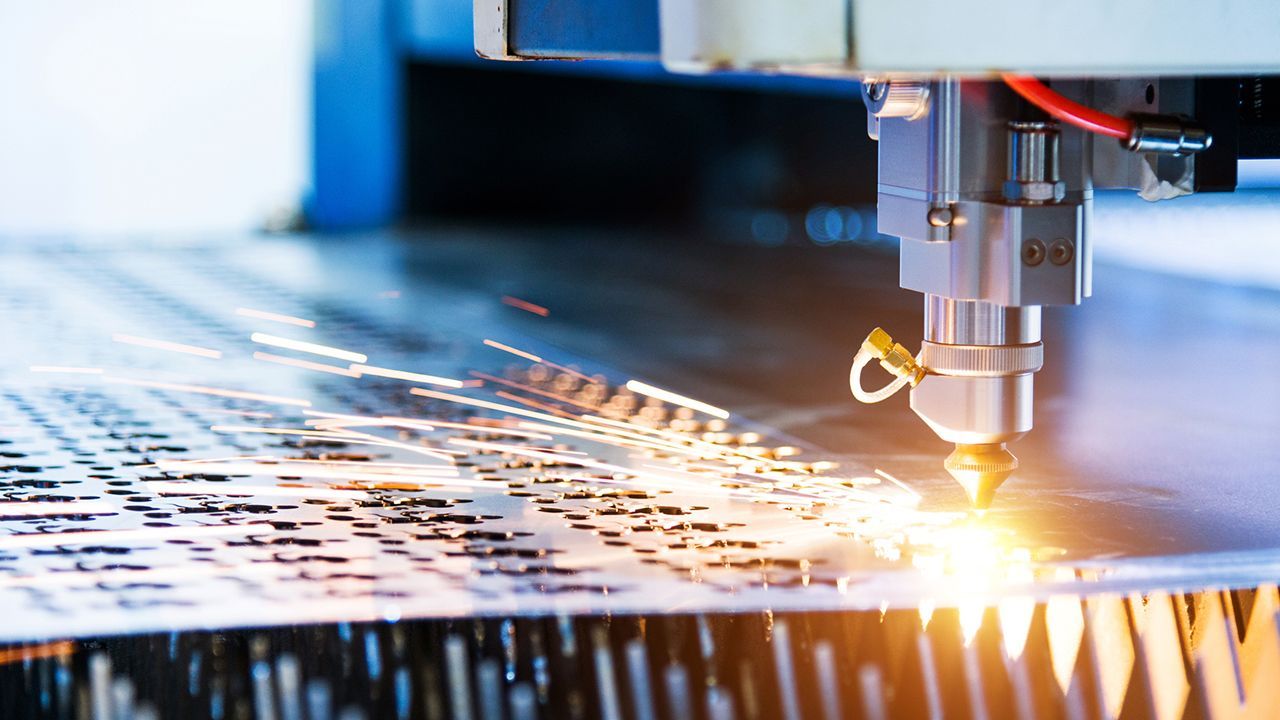